Parámetros de Operación necesarios para desarrollar las propiedades mecánicas y estándares de calidad del conformado para plásticos a través de la síntesis de polietileno de alta densidad.
Buen día, comunidad de steemit. Hoy les quiero presentar un post en el que representare los parámetros necesario para llevar a cabo el proceso de polimerización de polietileno de alta densidad en la industria, con el fin de dar continuidad a una publicación realizada hace algunos días, el cual podemos ver haciendo click aqui en el que se pudo explicar el desarrollo de esta ingeniería conceptual del proceso de conformado de plásticos a través de dicha síntesis.
Parámetros de Operación necesarios para desarrollar las propiedades mecánicas y estándares de calidad del conformado para plásticos a través de la síntesis de polietileno de alta densidad (PEAD).
En función de ampliar con la suma eficiencia posible un evento que encierra el proyecto para el moldeo por inyección efectivo de piezas con Polietileno de Alta Densidad es necesario tomar en consideración una serie de parámetros:
• MASA
Para la manufactura de cualquier producto se parte del principio que establece que la masa sólo puede sufrir transformaciones en el universo pero ni se crea ni se destruye. Es decir, en el presente ámbito aplica en la interpretación para la materialización de bienes generados a partir de la misma cantidad de materia prima que se agregue.
Por cada máquina de ciclo de moldeo por inyección con previo diseño de molde se requiere 482 gr / 1,06 Lbs. de Polietileno de Alta Densidad (PEAD), para hacer mas sencilla la explicación se utilizara como ejemplo la fabricación de un casco de seguridad con las especificaciones traídas a colación con anterioridad. Existe la posibilidad que por defectos en el diseño del molde con conductos demasiado grandes, presiones muy elevadas con respecto a la fuerza de sujeción, temperaturas excesivamente superiores y tamaños de la inyección irregular se generen rebabas o escorias de plásticos en la pieza moldeada, generando con ello una pérdida de material y defecto en el casco. En ese sentido se considera un margen del 2% de holgura en material.
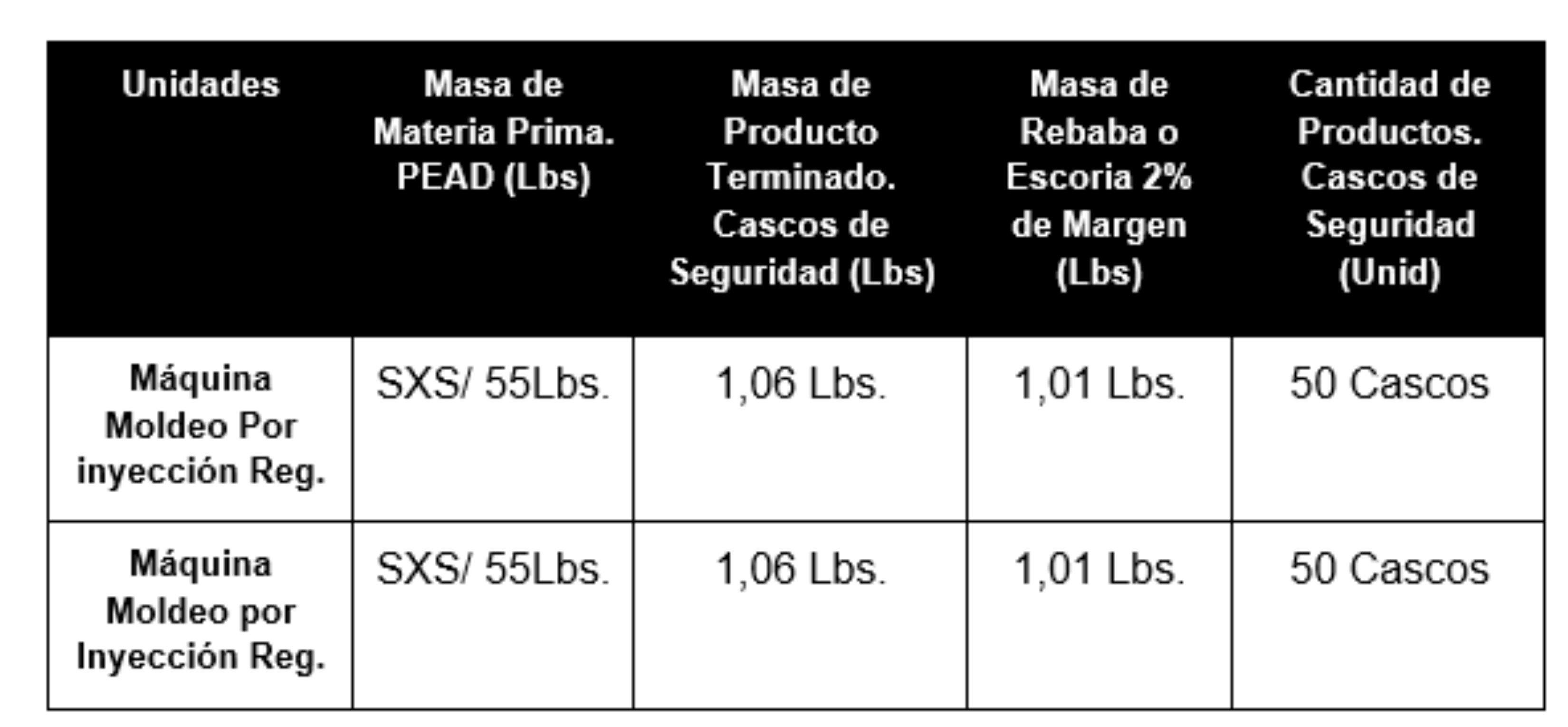
Tabla 1. Cantidad de Producto requerida para las operaciones de moldeo
Fuente:@ejrangel
• CONTRACCIÓN
Se denomina con tal término al fenómeno que sufren los polímeros termoplásticos de reducir su volumen durante su enfriamiento en el molde. Existe, incluso el caso de reducción por contracción volumétrica de hasta el 10% después de la inyección en el molde, dependiendo del material. Es de suma importancia conocer el valor de contracción de acuerdo al compuesto específico que se moldeará para optimizar las especificaciones en las dimensiones del mecanizado del molde y obtener con ello mejores resultados en la pieza final.
Vale destacar que cada valor de contracción en distintos componentes depende exponencialmente de la densidad o relación de masa en volumen y propiedades fisicoquímicas que posee cada uno. Un compilado comercial de referencia es el siguiente:
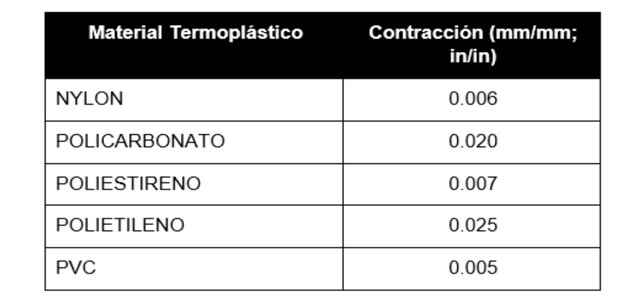
Tabla 2. Coeficiente de Contracción de materiales
Es decir, que en el caso del moldeo por Inyección de Cascos de Seguridad con las dimensiones previamente mencionadas y una composición de Polietileno de Alta Densidad se requiere compensar la contracción diseñando dimensiones de la cavidad del molde más grandes a las dimensiones requeridas por la pieza, validándose de la siguiente ecuación:
Ecuación N°1

Donde,
Dc= Dimensiones de la cavidad
Dp= Dimensión de la pieza moldeada
S= Valores de Contracción del Material
El casco de seguridad previamente especificado requiere de las siguientes dimensiones:
Alto (Һ) = 15 cm / 5.91 in
Ancho (A) = 21 cm / 8.27 in
Diámetro (Ø) = 23.5 cm / 9.25 in
Tomando en consideración estos valores las dimensiones del molde deben ser las siguientes:
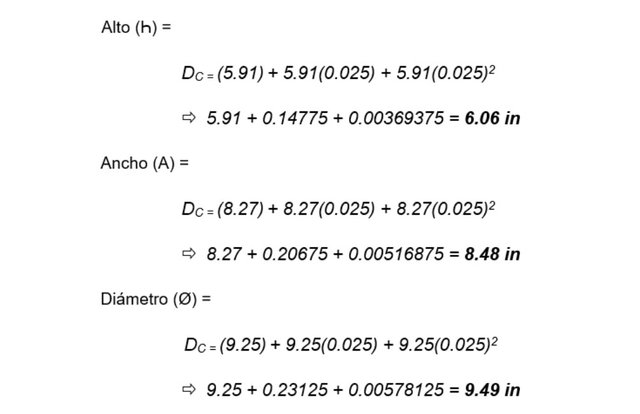
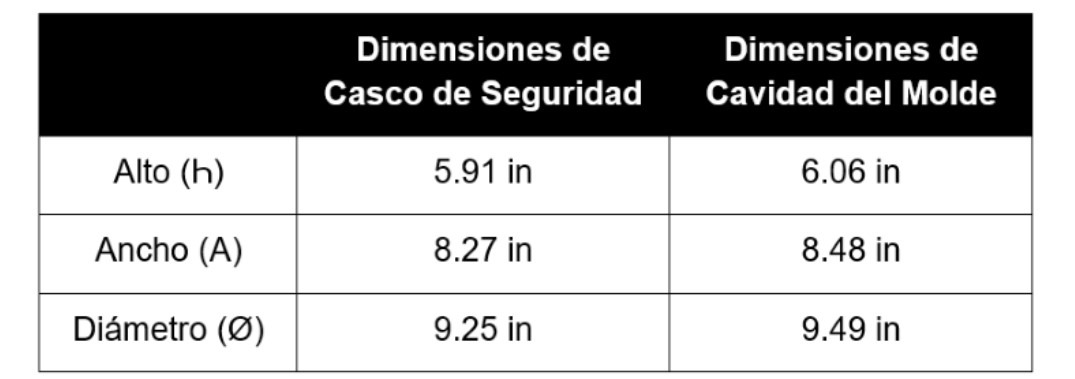
Tabla 3. Dimensiones del producto y del molde.
Fuente:@ejrangel
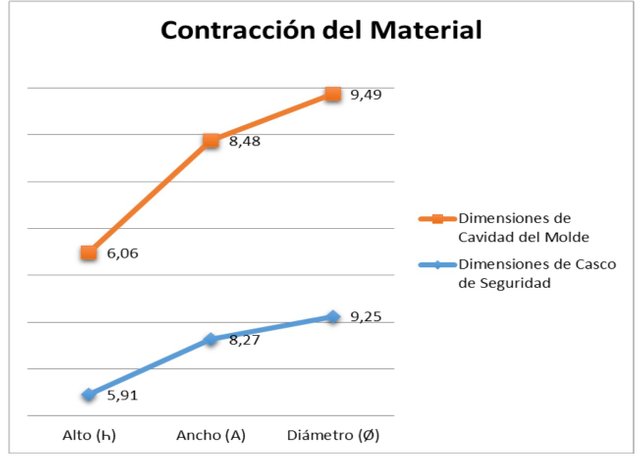
Figura 1. Relación de Contracción del PEAD en el Moldeo por Inyección.
Fuente: @ejrangel
• RELACIÓN PRESIÓN / FUERZA
De acuerdo a este parámetro sumamente importante en las operaciones, se establece el tonelaje o la capacidad instalada que se requiere por parte de una máquina para manufacturar la pieza final; en este caso, un casco de seguridad con las dimensiones ya mencionadas. Comercialmente, existen máquinas desde 10 Ton y 4.400 Ton que proporcionalmente poseen una capacidad de fuerza mayor para soportar presiones en la unidad de sujeción del ciclo.
En este caso, se requieren máquinas que superen las 1.000 Ton; pues se necesitan 1.06 Lbs de material inyectado en cada molde con dimensiones que en promedio superan las 9.5 in con presiones de hasta 290 Mpa. En ese orden de ideas, de acuerdo a cada una de las fases que comprende el proceso se van estableciendo diferente patrones de presión ejercidas fundamentalmente dentro del molde por la unidad de sujeción después de la inyección y generado por la resistencia que ejerce el flujo a fluir con las altas viscosidades del termoplásticos al alcanzar las temperaturas deseadas a través de los diámetros de circulación en la cavidad de inyección y del molde.
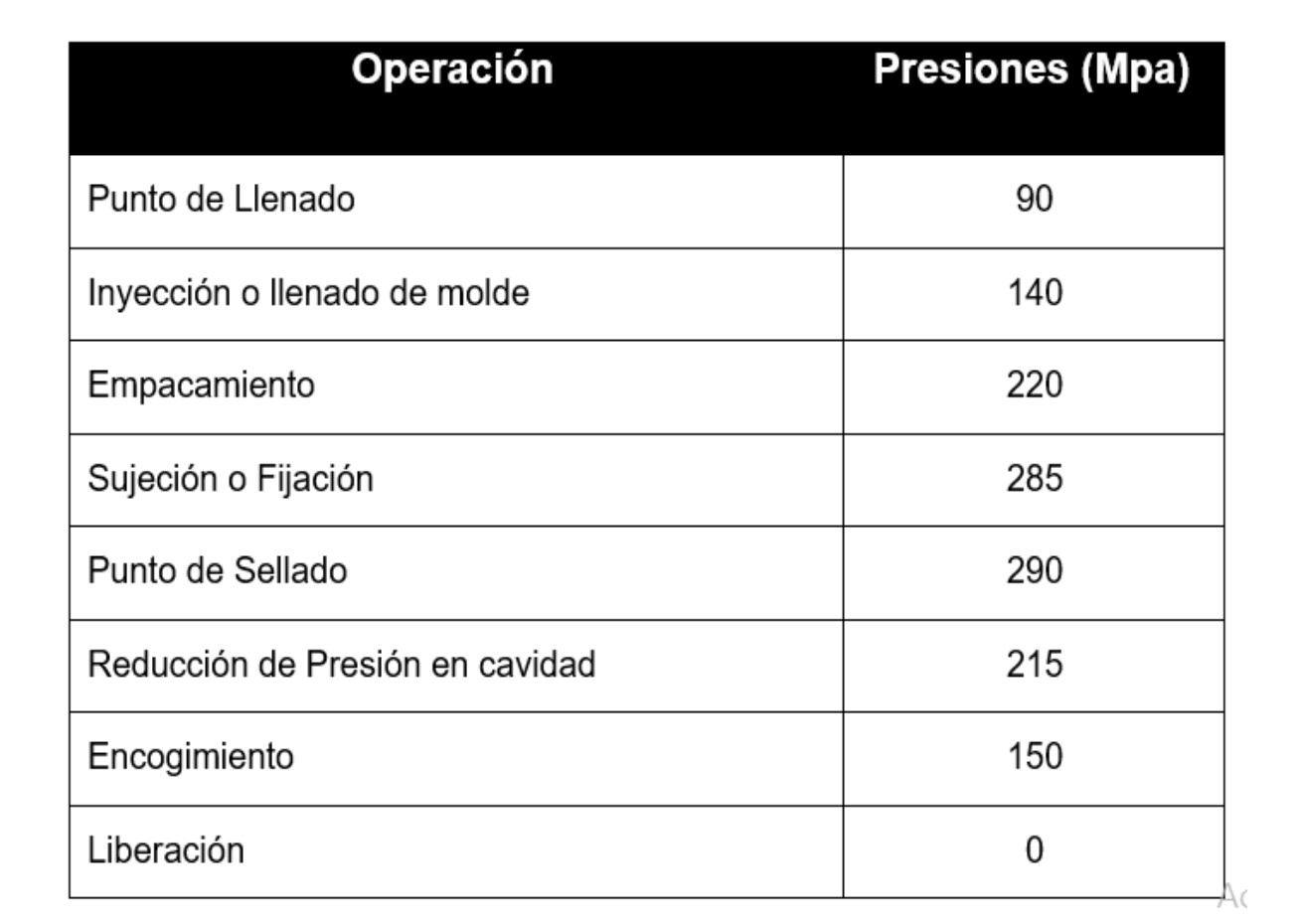
Tabla 4. Presiones por Operación del ciclo en Unidad de Sujeción
Fuente:@ejrangel
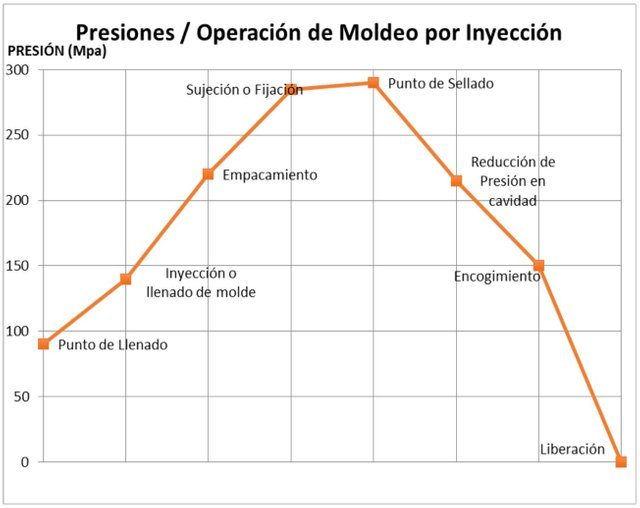
Figura 2. Relación de Presiones por Operación del Ciclo en Unidad de Sujeción.
Fuente: @ejrangel
Adicionalmente, para mantener estas presiones dentro de los intervalos de la Unidad de Sujeción de la máquina se ejerce una fuerza hidráulica a través del cilindro de sujeción de acuerdo a su tonelaje. Esa fuerza, viene expresada por medio de la Ecuación
Ecuación N°2:
F= Pm x Ap
Donde,
F= Fuerza ejercida (KN)
Pm= Presión media o promedio (KPa)
Ap= Área Proyectada (m2)
Se calcula el área proyectada de la pieza moldeada con los parámetros de las dimensiones conocidas:
Ecuación N°3:
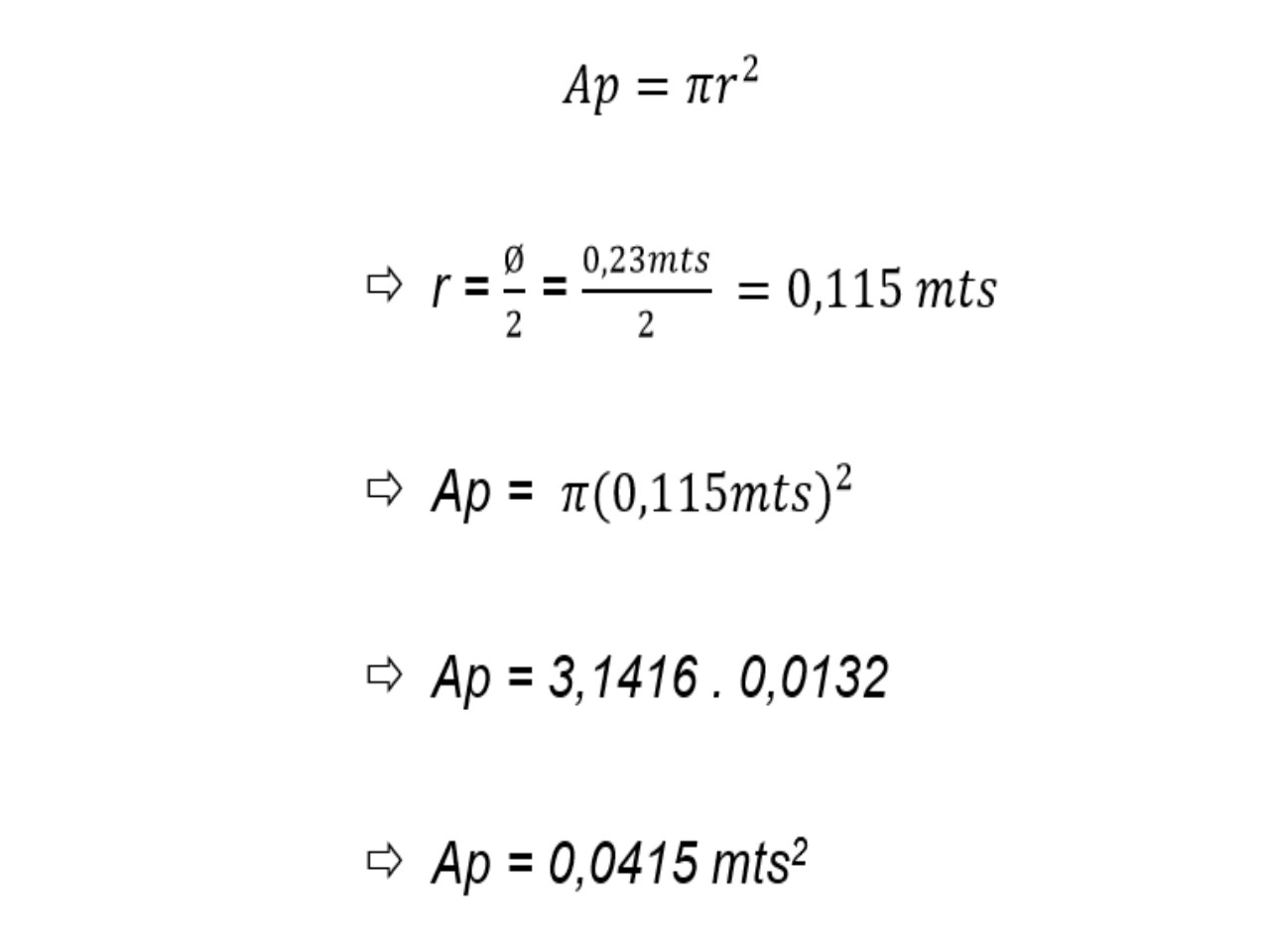
Por su parte, la presión media donde se ejerce la fuerza de sujeción es calculada en promedio de las presiones de dichos intervalos:
Ecuación N°4:

Se obtiene la fuerza requerida por la Unidad de Sujeción para ejercer las presiones de operación sustituyendo:
F= Pm x Ap
F = 198571 Kpa . 0,0415 mts2
F = 8241 KN.
• TEMPERATURA
Es posiblemente, el parámetro más importante en la efectividad de la operación con resultados satisfactorio. No es un valor constante, y puede ser regulado por la máquina dependiendo de la materia prima con la que se quiera trabajar. Cada polímero termoplástico varía en sus temperaturas de acuerdo a especificaciones del proveedor (según el peso molecular, ramificación del polímero, polidispersidad, conductividad térmica, propiedades termodinámicas y aditivos) y debe sugerir dichas variaciones con respecto a propiedades como índice de fluidez y temperaturas de trabajo.
En cualquiera que corresponda el caso, el procedimiento sugiere interpretar en cada material termoplástico la temperatura requerida para alcanzar el punto de fusión que baje sus propiedades de dureza, rigidez, porcentaje de elongación y densidad al mismo tiempo que estabiliza su viscosidad a un punto que permita la fluidez por medio de la cavidad de la boquilla de la inyección y hasta las cavidades del molde. Básicamente, se conocen en cada uno de los polímeros termoplásticos diferentes temperaturas de Fusión:
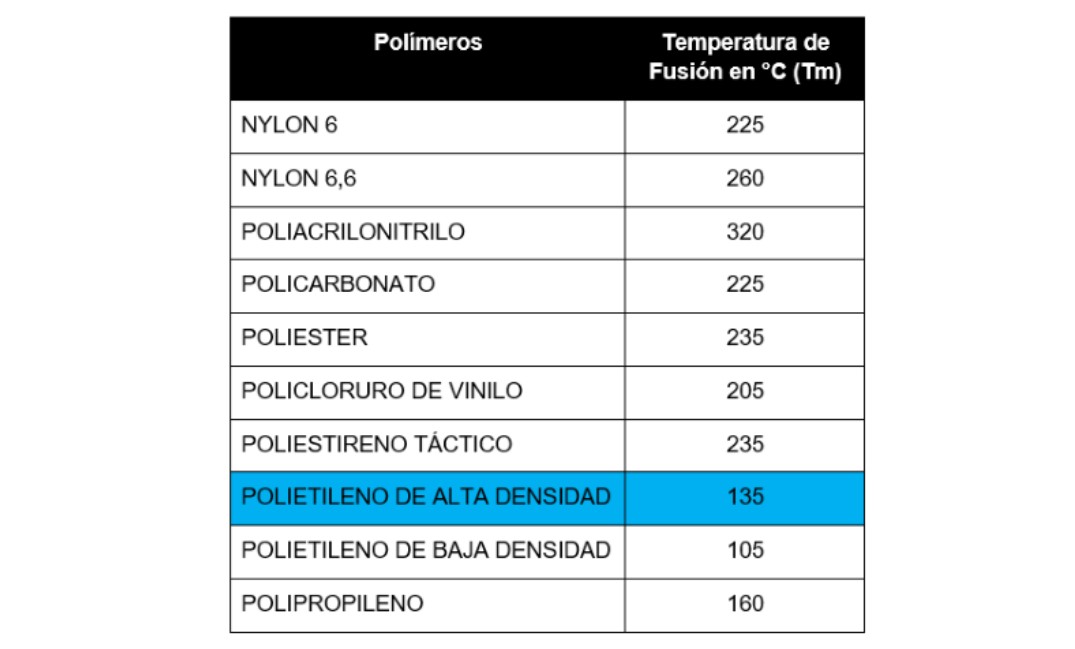
Tabla 5. Puntos de Fusión comunes en materiales termoplásticos
Fuente(imagen editada)
Tomando en consideración estos puntos estimados, se estipula en el procedimiento por intervalos del ciclo para la manufactura de un casco de seguridad con polietileno de alta densidad las siguientes temperaturas:
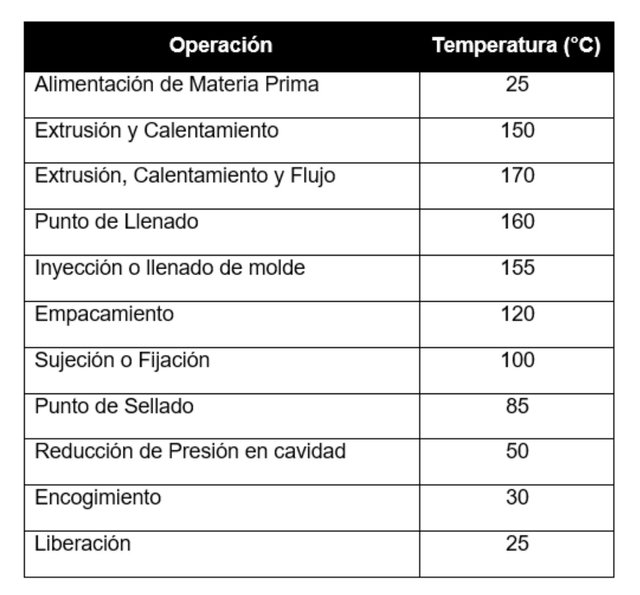
Tabla 6. Temperaturas por Operación del ciclo de Moldeo.
Fuente: @ejrangel
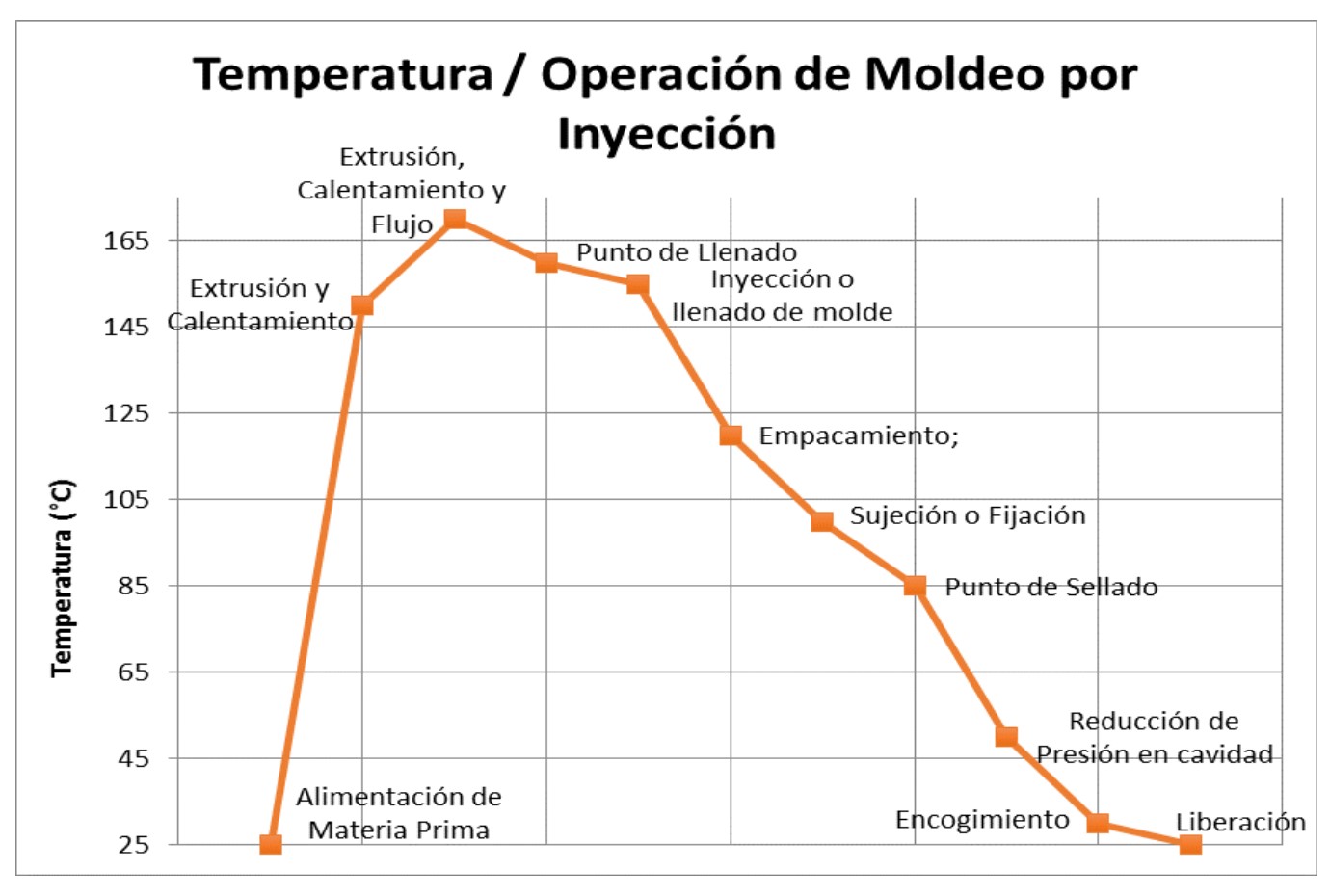
Figura 3. Relación de Temperaturas por Operación del Ciclo de Moldeo.
Fuente: @ejrangel
Vale la pena destacar, que la caída en la temperatura luego de la inyección del flujo termoplástico se debe al sistema de refrigeración en el molde de la máquina con el paso de aire y agua en cavidades y conductos estrechos en la superficie de separación con 0.001 in de profundidad y de 0.5 a 1 in de ancho aproximadamente; evitando con esa dimensión por la viscosidad del material que el polímero fluya a través de ellos y que se obtenga las condiciones ideales con el enfriamiento de dureza, rigidez y densidad.
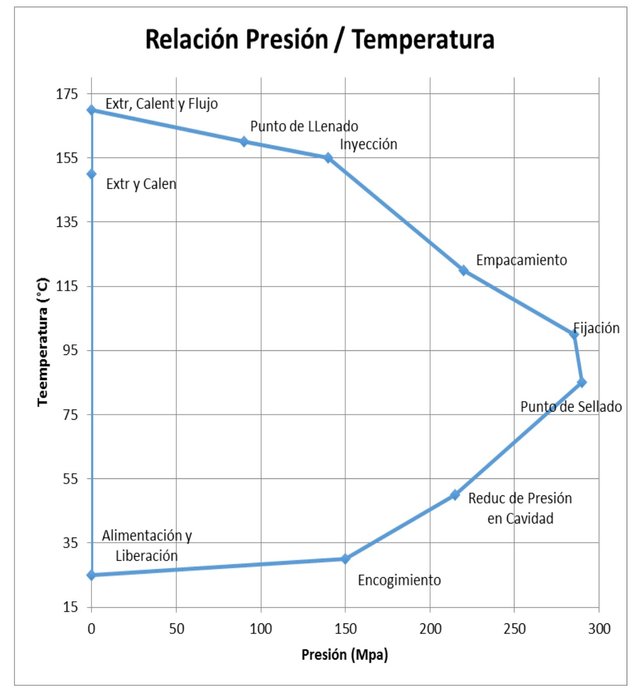
Figura 4. Relación de Presión / Temperatura por Operación del Ciclo de Moldeo.
Fuente: @ejrangel
• CAPACIDAD DE PRODUCCIÓN
Con los parámetros previamente establecidos para el ingenio conceptual de un proceso de conformado para cascos de seguridad a través de la síntesis del polietileno de alta densidad es comprobable que una maquina con el ciclo de moldeo por inyección posee la capacidad instalada de producir hasta 2 piezas por cada minuto.
De acuerdo a la factibilidad económica que respalda la demanda industrial se sugiere la instalación de:
- 2 líneas de producción (MPI; MPII)
- 3 máquinas de 1.000 ton por cada línea de producción
- 120 cascos por hora por cada máquina
- 720 cascos diarios por cada máquina
- 2.160 cascos diarios por línea de producción
- 4.320 cascos diarios en total
Asimismo, se toma en consideración la versatilidad del proceso instalado; ya que cada máquina que cumple el ciclo de moldeo por inyección para el conformado de plástico puede cambiar el mecanizado de sus moldes para fabricar piezas con otras dimensiones y especificaciones; ajustando los parámetros y propiedades fundamentales.
Referencias:
- https://portalacademico.cch.unam.mx/alumno/quimica1/unidad1/reaccionesQuimicas/leyconservacionmateria
- http://www6.uniovi.es/usr/fblanco/Leccion10.PLASTICOS.Extrusion.2005.pdf
- https://books.google.co.ve/books?id=tcV0l37tUr0C&pg=PA335&lpg=PA335&dq=Donde,++Dc%3D+Dimensiones+de+la+cavidad++Dp%3D+Dimensi%C3%B3n+de+la+pieza+moldeada++S%3D+Valores+de+Contracci%C3%B3n+del+Material&source=bl&ots=7ZLD96cCYt&sig=JhemPhDgoSbtDJ8qDl4x4r00H8U&hl=es&sa=X&ved=0ahUKEwjX0YLUjLbZAhWhxFkKHU84BoMQ6AEIJjAA#v=onepage&q=Donde%2C%20%20Dc%3D%20Dimensiones%20de%20la%20cavidad%20%20Dp%3D%20Dimensi%C3%B3n%20de%20la%20pieza%20moldeada%20%20S%3D%20Valores%20de%20Contracci%C3%B3n%20del%20Material&f=false
- https://www.plenco.com/plenco_processing_guide_spanish/Sect%2010%20BMC%20Injection%20Startup%20Procedure%20(Spanish).pdf
- http://ocw.usal.es/ensenanzas-tecnicas/materiales-ii/contenidos/PLASTICOS.pdf
- https://flacofidel89.wordpress.com/2013/05/21/procesos-de-conformado-para-plasticos-2/
Siendo un SteemStem Estados
Congratulations @ejrangel! You have completed some achievement on Steemit and have been rewarded with new badge(s) :
Click on any badge to view your own Board of Honor on SteemitBoard.
For more information about SteemitBoard, click here
If you no longer want to receive notifications, reply to this comment with the word
STOP
hola hola... siguiendote por aqui, muy interesante tu publicacion.